今回は、「セラミックコンデンサ」についての説明です。
1.セラミックコンデンサとは?
セラミックコンデンサとは、名称通り誘電体にセラミック(陶磁器のこと、無機物を加熱処理し焼き固めた焼結体)を使用した無極性のコンデンサのことです。
セラコンと略して呼ぶことが多いです。
無極性とは、コンデンサの端子にプラスとマイナスの区別が無いことを指しています。
コンデンサには端子が2つ存在しますが、セラミックコンデンサの場合はどちらに電圧を印加しても問題無いのです。
形状による種類分けは、円板型と積層型の2種類があります。
円板型は単板型とも呼ばれ、以下のような形状をしています。
大体橙色か水色で丸い形状をしていて、プリント基板にあらかじめ用意しておいた穴(スルーホール)に足(リード)を挿し込んで基板の裏側からはんだで固定する…いわゆるリードタイプです。
積層型は主に以下のような形状をしています。
直方体で基板表面に実装するタイプ(SMTタイプ)のものが多いです。
多いと言ったのには理由があり、一見単板型に見えるようなタイプも積層型だったりするのです。
(上図右のようなタイプ)
円板型(単板型)はリードタイプのみ、積層型はリードタイプとSMTタイプがあるんですね。
中でも、チップ型の積層セラミックコンデンサはあらゆる電子機器に使用されていて、一つの基板に数百個搭載されていることも珍しくありません。
2.積層セラミックコンデンサの構造
一番一般的な積層セラミックコンデンサの構造について説明していきます。
積層セラミックコンデンサは、名称通り“積層”構造になっています。
具体的には、電極と誘電体が交互に多重積層されています。
積層セラミックコンデンサの断面図は以下のようになっています。
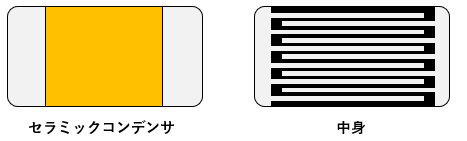
灰色部分が内部電極、黒色部分が誘電体層です。
実装時にはんだ付けを行う電極が左右に配置されていて、この電極は実は内部に向かって延びています。
そこで、右側の電極ー誘電体ー左側の電極という順番に配置したものをいくつも積み重ねているから積層型というわけです。
この構造は複数のコンデンサを並列に接続していることに等しいです。
電極に誘電体を挟んだもの(=コンデンサ)が横並びになっていますからね。
並列接続時のコンデンサの静電容量は単純に足し算になるので、全容量の合計が合成静電容量となるわけです。
「平行板コンデンサの静電容量」は以下の式で表されました。

※静電容量C[F]は、誘電率ε[F/m]と導体板の面積S[m2]に比例し、導体板間の距離d[m]に反比例する。
セラミックコンデンサに関しても根本的な考え方は変わらないです。
この公式に積層数Nをかけるだけです。
その為、電極の面積が大きく、電極間距離が短いほど静電容量は増加します。
以上より、積層型形状は小型且つ大容量という理想を叶えてくれる構造となっています。
3.積層セラミックコンデンサの製造工程
積層セラミックコンデンサの製造方法は微妙に色々な種類があります。
ただ、どの方法も大きな流れは変化しないので、主流かと思われるグリーンシート工法(ドライ工法)についてざっくりと説明していきますね。
①誘導体のシートを形成する。
キャリアフィルムの上にペースト状にしたセラミック製誘導体を薄く引き伸ばして乾燥させます。
このシートをグリーンシートと呼びます。
この”グリーン”は“緑”ではなく“生”という意味です。
②内部電極を印刷する。
グリーンシート上にペースト状の電極材料を印刷(配置)します。
要するに同じ型の電極をまとめて配置します。
電極パターンを形成するマスクを用いて一度に印刷できるので、量産に向いています。
③シートを積層してプレスする。
印刷した電極がうまく重なるようにシートを積層した状態でプレスして、一体成型をする。
この工程で電極と誘電体が交互に多重積層されるわけです。
ちなみに、積層数は数百数千レベルで行われます。
④積層したシートを切り分ける。
一体成型した積層シートを決められたサイズに切り分けてチップ状にします。
ここで積層セラミックコンデンサらしい見た目に近づきます。
⑤焼成する。
切り分けたチップを焼成炉に入れて約1000~1300℃で焼き上げます。
焼き上げたチップは硬くなります。
⑥外部電極を形成する。
露出している内部電極に外部電極の材料をペーストし、再び焼き上げます。
⑦メッキ処理をする。
ニッケルメッキ及びスズメッキを施します。
通電することでメッキ処理を行います。
ニッケルメッキは信頼性向上、スズメッキははんだ実装を容易にするために行います。
⑧検査後包装する。
4.セラミックコンデンサの特徴
セラミックコンデンサの特徴としては、以下のようなものが挙げられます。
- 無極性。
- 小型ながら静電容量範囲が広い。
- 高耐熱性。
- 長寿命。
- 低ESRなので発熱しにくい。
- 低ESLによる高周波領域での安定動作が可能。
- 温度変化により静電容量が変化する。
- 印加電圧により静電容量が変化する。
実際のコンデンサには抵抗成分(ESRと言う)やインダクタ成分(ESLと言う)が存在し、セラミックコンデンサはESRもESLも低めになる傾向があります。
セラミックコンデンサの場合は、ESRが小さいので発熱しにくいです。
また、ESLが小さいと共振周波数が高くなるので、高周波数帯でも問題なく使用ができます。
この辺りの詳しい説明は次回行います。
温度変化によって静電容量が変化するのはコンデンサ共通の特性ではあるのですが、セラミックコンデンサは使用する誘電体の種類によって静電容量の変化率が大きく異なります。
公的な規格でClass1(温度補償用積層セラミックコンデンサ/低誘電率系積層セラミックコンデンサ)、Class2(高誘電率系積層セラミックコンデンサ)と分類されていて、Class1の方が温度特性は良いです。
また、印加電圧による静電容量の変化(DCバイアス特性)に関してもClass1ではほとんど発生しません。
誘導率が高くなる代わりに温度特性とDCバイアス特性が悪くなるんですね。
以上、「セラミックコンデンサ」についての説明でした。