今回は、「基板の初歩的な用語」についての説明です。
目次
1.初めに
身の周りには色んな電化製品があります。
冷蔵庫・電子レンジ・洗濯機・掃除機・ドライヤー…生活必需品の多くは電化製品です。
そんな電化製品の中には、必ず基板と呼ばれる緑の板が入っています。
厳密にはプリント基板と呼ぶのですが、基板と省略されていることが多いです。
一言に基板と言っても、基板を構成する要素には様々な名称が付いています。
本記事では、初歩的でよく聞くことになるであろう用語の意味を簡単にまとめてみました。
基板について学ぶ前に軽く目を通しおくと良いかと思います。
2.用語説明
この記事で紹介している用語は以下の通りです。
普通に「数字」→「アルファベット」→「ひらがな・カタカナ・漢字の読み仮名で五十音順」という並びにしています。
PCB
部品実装後のプリント基板のこと。
[Printed Circuit Board]の略称です。
PWBに部品を実装したらPCBになります。
詳しくは以下の記事を参照。
PWB
部品実装前のプリント基板のこと。
[Printed Wired Board]の略称です。
PWBに部品を実装したらPCBになります。
生基板とも呼ばれる。
詳しくは以下の記事を参照。
Vカット
捨て基板の切り離しをサポートするV字型の溝のこと。
板チョコとかアイス最中の溝みたいなものがプリント基板にもあるイメージです。
ラジオペンチなどで捨て基板部分を挟んで捻るとVカットに沿って簡単に切り離しができるようになっています。
素手でもいける。結構気持ちいい。
Vカットは端面から端面までの直線にしか入れることができないので、円形にVカットを入れるなどの器用なことはできません。
円形にしたい場合は、Vカットではなくミシン目(スリット)という手法を用います。
ミシン目もVカット同様に捨て基板の切り離しのために設けるものですが、Vカットはバリが残らない綺麗な面を得られる反面コストが高くなります。
エッチング
プリント基板製造時に必要な銅箔回路パターン以外を溶かして取り除く工程のこと。
露光及び現像という手法により、必要な回路パターンだけフィルムで保護されていて、それ以外は銅箔が剥き出しの状態になります。
この剥き出しの銅箔部分を薬剤で溶かして除去する工程がエッチングです。
ちなみに、プリント基板の製造工程は「露光→現像→エッチング→黒化処理」の順番で行われます。
詳しくは以下の記事を参照。
ガーバーデータ
プリント基板を作るために必要なデータのこと。
パッドやランドなどの部品配置情報・層数情報・層ごとのパターン配置情報・シルク情報などのデータが該当する。
ガーバーデータは、P板.comのようなプリント基板製造会社にプリント基板製造依頼を出すときに一緒に渡します。
すると、ガーバーデータを基にしてCAMで実際の製造に必要な形式のデータに編集され、プリント基板の製造に活用されます。
クリアランス
パターンとはプリント基板上の電気を通す配線のことなので、機器を接続するケーブルと同じような役割をしています。
ケーブルは感電しないように絶縁体で覆われていますよね?
あの絶縁体被覆があるので、ケーブルは束ねて使用することができます。
では、並走するパターンがあったとして、それらのパターンをケーブルのように絶縁保護するにはどうすれば良いでしょうか?
A.パターン間にクリアランス(距離・間隔)を設ければ良い。
ということで、プリント基板のパターンはその経路ごとにクリアランスが設けられています。
各経路が放射するノイズなども考慮する必要があるので、「GNDパターンからは3mm以上のクリアランス(距離)を空けて信号パターンを配置する」という具合に、回路設計者はしっかりと考慮する必要があります。
ちなみに、医療分野にもクリアランスという用語は存在しますが、意味は全く異なります。
黒化処理
プリント基板製造時にエッチングした後の回路パターンを描いている銅箔表面を酸化処理してわざと粗くすることで積層時に密着しやすくする工程のこと。
酸化処理すると黒く変色するから黒化処理と呼ばれます。
新品の10円玉に対して使い古した10円玉が黒ずんでくるのを想像してもらえば良いかと思います。
ちなみに、プリント基板の製造工程は「露光→現像→エッチング→黒化処理」の順番で行われます。
詳しくは以下の記事を参照。
現像
プリント基板製造時に露光させた部分以外の余分なドライフィルムを溶融除去する工程のこと。
露光により、必要な回路パターンに沿って銅箔表面に貼り付けたフィルムが硬化します。
ここで硬化していない不要なフィルムを溶融除去させるのです。
ちなみに、プリント基板の製造工程は「露光→現像→エッチング→黒化処理」の順番で行われます。
詳しくは以下の記事を参照。
サーマルランド
はんだ付けの際、熱がパターンに逃げてはんだが溶けにくくなるのを防ぐためにパターンとの間に切り込みを入れたランドのこと。
普通のランドは穴(スルーホール)の周囲を覆っているので円形状の銅箔になっているのですが、サーマルランドは以下のように切り込みを入れてあります。
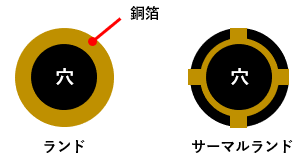
こうすることではんだ小手の熱がパターンに逃げにくくなるので、はんだ付けがしやすくなります。
GNDパターンのような太いベタパターンに対してはサーマルランドにしてあることが多いです。
ただし、パターンとの接触箇所が減ることによって抵抗値が増加するので、電流量によってはあえて通常のランドにする必要があります。
ちなみに、サーマル[thermal]には[熱的]という意味がありますので、サーマルランドは「熱について考慮したランド」というイメージになります。
シルク
プリント基板に印刷された文字や図形のこと。
簡単に言えば、プリント基板に対するメモ書きみたいなものです。
部品外形や部品番号などを表示することで、どの位置に何をはんだ付けすれば良いか見てわかるようになります。
特に、ICやコネクタなどは1ピンがどこに位置するかを指定することで取り付け向きを間違えないようにしていることが多く、シルクは最早無いと困るレベルの必需品となっています。
ちなみに、一般的には白色です。
捨て基板
プリント基板から切り離して捨てる不要部分のこと。
プリント基板を作ろうとした場合、最初は絶対に長方形になります。
なのですが、スペースの関係で台形・円形・T字・L字など、様々な形状で使いたいことはよくあります。
そこで、長方形から余計な分を切り離せるような形にしており、この時に不要となる部分が捨て基板となります。
ここまでのイメージだと捨て基板はただのゴミというイメージですが、有効活用している事例もあります。
捨て基板部分に同じ種類の基板でも部品の実装/未実装の違いを設けていることが判別できるような管理No.を印字しておくなどです。
捨て基板を切り離すための加工の種類にはミシン目とVカットという手法があります。
スリット(ミシン目)
捨て基板を切り離すために設けられた幅2mm程度の細長い切り抜き穴のこと。
また、パターン間の絶縁距離確保のために使用することもあります。
端的に言えば隙間のことなのでスリット、もしくはミシンで裁縫した際の模様と似ているからミシン目と呼ばれています。
例えば、円形のプリント基板を製作依頼したとします。
ですが、プリント基板を最初から円形にすることは不可能で、どんな形状にするにせよ長方形(正方形を含む)から切り抜いて使用することになります。
つまり、プリント基板としては不要な部分(捨て基板)が出てくるわけです。
そんな時にミシン目が活躍します。
円形にする上で邪魔になる捨て基板の部分をミシン目で隔てることにより、部分的に繋がっている箇所を素手でへし折るだけで円形のプリント基板を得られるようになります。
ただ、その部分的に繋がっている箇所がバリとして残ることには注意が必要です。
ちなみに、バリが出る箇所を使用するプリント基板側にめり込ませることにより、バリが干渉しないように対策していることが多いです。
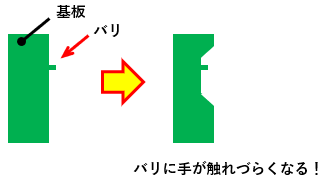
バリを残さずに綺麗に直線に切り離す手法にVカットというものがあるため、状況に応じて使い分けます。
※ ただし、Vカットの方が高コスト。
スルーホール(TH)
ランドの中心にある穴のこと。
[Through Hole]を略してTHと呼ぶことが多い。
DIPタイプの部品の足(リード)を通してはんだ付けをするための穴。
要するに、電子部品固定用の穴です。
その為、穴の周りには銅箔部分が存在します。
それに対し、周りに銅箔部分が存在しない穴のことはノンスルーホールと呼ぶ。
ソルダーレジスト
プリント基板のパターンを覆うように塗られた耐熱性・絶縁性ありの緑色のインクのこと。
単にレジストと呼んでいることもあります。
基板によっては青色だったり赤色だったりしますが、一番安いのが緑色なので緑色が最も一般的となっています。
ソルダー=はんだ、レジスト=抵抗なので、はんだの付着に対して抵抗を持っている物質を指しています。
パッドやランドのような銅箔を露出させる必要のある部分以外にソルダーレジストを塗ることで、部品実装時に余計な部分にはんだが付着しないようにしています。
ちなみに、絶縁していると言っても非常に薄い膜状になっているだけなので、金属で触れるのは控えるべきです。
また、ほこりや湿気といったストレスからもパターンを守る働きがあります。
ノンスルーホール(NTH)
ランドの存在しないただの穴のこと。
[Non Through Hole]を略してNTHと呼ぶことが多い。
要するに、ねじを通して基板を固定したりする際に使用する穴です。
その為、穴の周りには銅箔部分が存在しません。
それに対し、周りに銅箔部分が存在する穴のことはスルーホールと呼ぶ。
パターン
プリント基板上に銅箔によって引かれた電気を通す配線のこと。
やろうと思えばカッターで回路を断絶させたりできる。
家には電気や水道などが供給されていますよね?
コンセントに電源プラグを挿して電化製品に電気が供給される、洗面台や風呂の蛇口から水が出る…当たり前のことですよね。
なんでこんなことが可能になっているのかと言うと、コンセントまでは電気が来るようにケーブル配線を、蛇口までは水が来るように配管をしているからです。
ここで言う家をプリント基板だと考えた時、ケーブル配線・配管がパターン、電化製品や風呂などが実装部品というイメージになります。
家は大きいのでケーブル配線や配管で繋げば良いのですが、プリント基板の場合は小さいのでそうもいきません。
そこで、場所を取らずに配線できるパターンが採用されているわけです。
ちなみに、ベタ塗りしたような太いパターンのことをベタパターンと呼びます。
パッド
SMTタイプ(表面実装タイプ)の部品をプリント基板にはんだ付けするための銅箔露出部のこと。
主に四角の形状をしています。
実装部品のデータシートにどんなサイズでパッド配置を設計すればいいかは載っています。
なので、『部品をここに実装する』と決めたら、データシートを閲覧してそのデータ通りにパッドを形成するようにしましょう。
パッドは結構簡単に剥がれるので、はんだ付けの際はパッドを温めすぎたり部品を強く引っ張らないように注意です。
ちなみに、CPUなどははんだ固定箇所が部品の真下にあったりするので、手実装は不可能だったりします。
はんだ
スズと鉛を主原料とした金属のこと。
溶けやすい金属なので、一旦溶かしてもう一度固めることでプリント基板に抵抗やコンデンサなどの電子部品を実装することができる。
最近は鉛が人体に有害だと言われているのでスズを主原料としていることが多い。
詳しくは以下の記事を参照。
半田面
プリント基板における裏面のこと。
部品面(表面)に配置したリード部品の足(リード)を固定する側の面のこと。
CAD上ではB面と表示されていることが多いです。
ちなみに、半田面の反対側は部品面と呼びます。
ビアホール
プリント基板の各層にあるパターン間を接続するための小さな穴のこと。
ビアと呼ばれることが多い。
ビア[via]には[経由・通じる]という意味がありますので、名称から意味はある程度想像できます。
プリント基板は多層構造にできます。
その別の層同士のパターンを繋ぐのがビアホールの役割なので、穴の大きさは非常に小さいです。
マチ針じゃ先端しか通らない程度には小さいです。
層ごとに存在するGNDパターンをすべて共通にする際などによく用いる。
6層などの多層構造になった場合、内層同士で接続されているだけだと外観からビアがあるのか判断できなかったりします。
また、基板全層を貫通するビアをスルーホールビア、基板の一部の層を貫通するビアをインナービアと呼びます。
インナービアの中に基板表面と内層を貫通するブラインドビア、基板の内層同士を貫通するベリッドビアが存在する。
分類は色々あるのですが、そこまで詳しく覚える必要は無いです。(参考として載せただけです)
部品面
プリント基板における表面のこと。
リード部品やでかくて重めな部品が実装されて物々しい見た目になっている方が部品面です。
なんでそうなっているのかと言うと、リード部品や重い部品を片面に集めないとリフロー処理ができないからです。
CAD上ではA面と表示されていることが多いです。
リフローとは、プリント基板に部品を実装するための主要な方式で、コンベアに載せたプリント基板を炉の中を通し、パターンに塗布しているはんだが融けてはんだ付けが完了するというものです。
リフローは表裏両方に行うことが多いのですが、リード部品や重い部品を両面に配置したらどうなると思いますか?
片面実装中にもう片面に実装してあった部品が落下します。
ということで、穴に挿すだけのリード部品や重い部品を部品面に集約しているのです。
一応接着剤を使ったりと対策をすれば裏面にリード部品を実装することもできますけどね。
※ SMTタイプ(表面実装タイプ)の部品は表裏関係無く実装されていることがあります。
ちなみに、部品面の反対側は半田面と呼びます。
プリント基板
樹脂でできた絶縁性の板の上に電線の代わりに銅箔で回路を形成(プリント)することで小型化し、様々な電子部品を実装するための基板のこと。
様々な部品をはんだ付けします。
詳しくは以下の記事を参照。
ベタパターン
プリント基板上に銅箔によって引かれた電気を通す配線であるパターンの内、ベタ塗りをしたように大きな面積となっているパターンのこと。
ベタと呼んでいることがある。
通常のパターンは信号を伝達したりするだけなのでそこまで電流が流れないのですが、電源やGNDのラインになると大きな電流が流れます。
パターンの太さは電流を流せる大きさに比例するので、電源やGNDのような大きな電流が流れると想定できるパターンはベタパターンになっていることが多いです。
実際、プリント基板の多層構造を利用して、内層一層分を丸ごと電源やGND用のベタパターンとして使用していることは多々あります。
ランド
DIPタイプ(リードタイプ)の部品をプリント基板にはんだ付けするためのに用意された銅箔部分のこと。
穴(スルーホール)の周囲にある円形状の銅箔部分を指しており、穴にリード部品の足を差し込んで、ランドにはんだ付けすることで固定します。
ただ、GNDパターンのような太いベタパターンだとはんだ小手の熱がパターンに逃げてはんだが溶けにくくなるため、パターンとの間に切り込みを入れたサーマルランドというものも存在します。
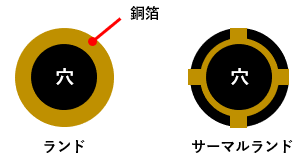
露光
プリント基板製造時に必要な銅箔回路パターンのみフィルムに焼き付ける工程のこと。
樹脂板の上に銅箔、銅箔の上にフィルムを貼り、その上にプリント基板の回路パターンを模ったマスクを重ね合わせて、紫外線を照射します。
すると、回路パターン部分にのみ紫外線が照射され、フィルムが反応して硬化します(焼き付けられます)。
ちなみに、プリント基板の製造工程は「露光→現像→エッチング→黒化処理」の順番で行われます。
詳しくは以下の記事を参照。
以上、「基板の初歩的な用語」についての説明でした。